VIDAR Augments Sludge Removal Process with New Continuous Operation Schedule
Fluctuating sludge build-up was causing frequent pump maintenance and efficiency challenges for the Metropolitan Council Environmental Services’ water/wastewater plant. Met Council treats the wastewater of 2.7 million citizens, which is about 250million gallons per day on average. They steadily achieve near-perfect compliance with both federal and state water discharge standards, plus hold customer rates approximately thirty five percent less than the national average.
Their interest in switching to a VFD solution was hindered by the plant’s underground location, which would require them to drill into the walls to accommodate the cable requirements associated with a VFD installation.
Processing Challenges
Met Council operated eight primary tanks, each equipped with two large sludge pumps (50HP and 100HP), which are switched depending on the season. When processing wastewater through the primary tanks, sludge consistently sank to the bottom due to the existing pump motors only being run once every four hours. Operators frequently used chemicals to break down built-up sludge in the tank, disrupting operations and increasing wear and tear on the machinery.
It became clear that continuous pumping at a slower speed was necessary to prevent sludge accumulation in the tanks and improve process control.
Infrastructure Issues
While a VFD would address the sludge issue, the underground infrastructure of the plant posed significant barriers. Met Council would need to drill into their walls to run cables throughout the massive underground operation. Installing a traditional VFD requires several new specially designed cables to be run to the motor terminal box, which can be very expensive as they must mitigate the consequences of harmful high frequency noise and voltage spikes. Ultimately, this was set to cost the company a multi-six figure sum.
Additionally, the underground location amplified the noise (105 dB) associated with running the current pumps.
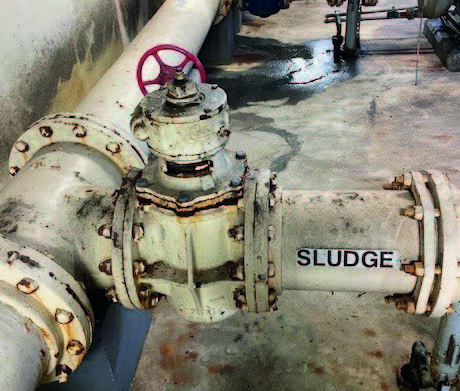
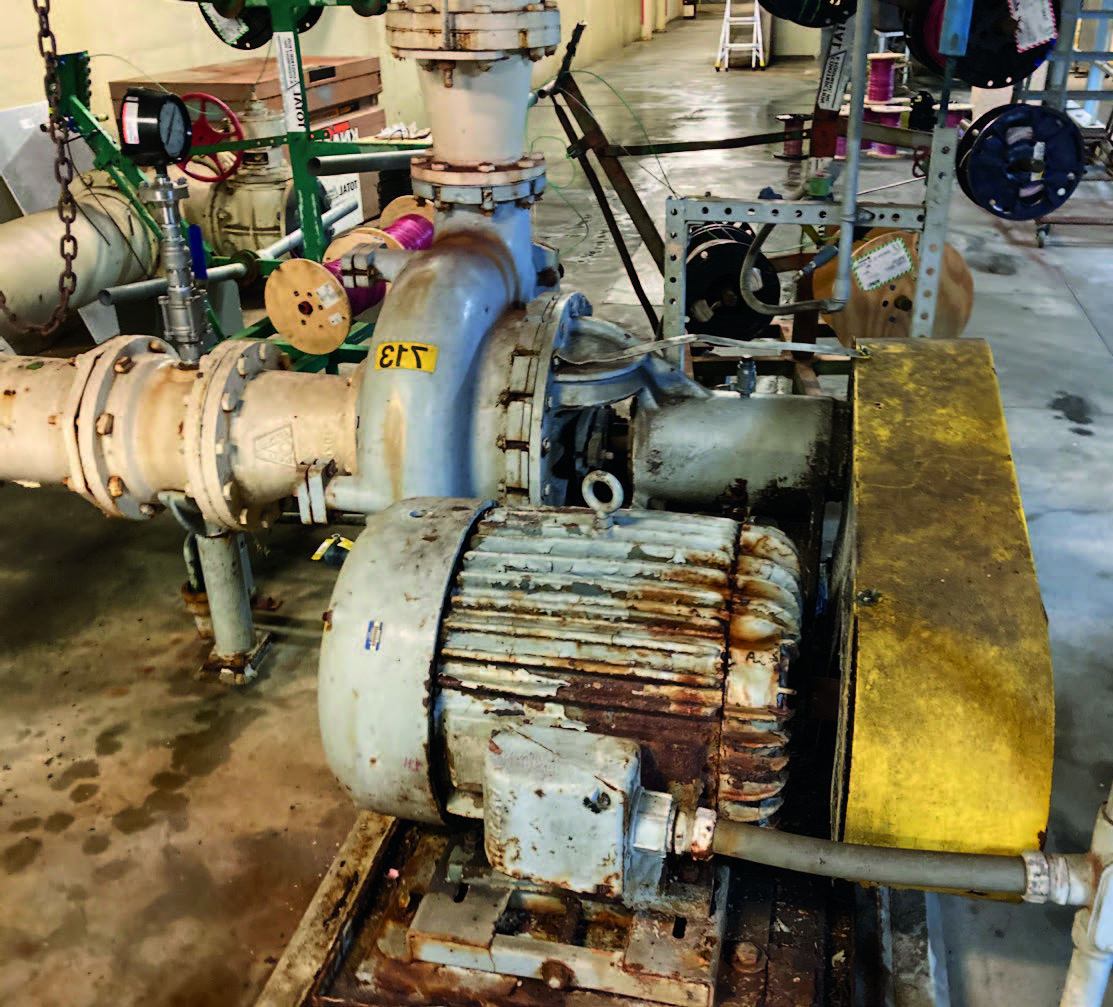
Acheived benefits
Saved space with simplified installation
Improved energy efficiency
Eliminated mechanical controls
Enhanced operations
Reduced downtime
Measurable Results
VIDAR and a constant pumping scheme increased process efficiency:
• Total Solids increased from 1% to between 2.5 – 3.5%
• Reduced workload for centrifuges upstream, extending their lifespan
• More effective dewatering/gravity thickening scheme
“One of the biggest benefits we’ve seen is the improved solids removal. When we first started sampling the sludge it was less than 1% Total Solids at the end of a 4 hour cycle. We are currently running between 2.5-3.5% TS using constant pumping. In the long term, if we had these motors on all the pumps and operated the same manner, that would aid SMB in their gravity thickening efficiency. The better dewatered the sludge is, the less we’re relying on the centrifuges to do. We may see a savings in their energy costs too, so that is something to keep in mind. We are not able to utilize current VFD technology due to space constrictions within our electrical room, these add a space saving solution.”
– Manager, Electrical Maintenance
Reduced Noise:
Ambient noise dropped from 105 dB to just 79 dB,allowing for safer operation.
The VIDAR Solution
To tackle these challenges, the company opted for VIDAR. In just four hours, two VIDARs were retrofitted onto the large sludge pumps, requiring no alterations to the plant’s infrastructure. Switching from an ON/OFF control scheme to a streamlined continuous one required a simple change in the SCADA system to run a speed reference to VIDAR. The 50HP VIDAR motors were set to run at just 648 RPM (a 55% speed reduction), allowing continuous sludge removal instead of once every four hours.
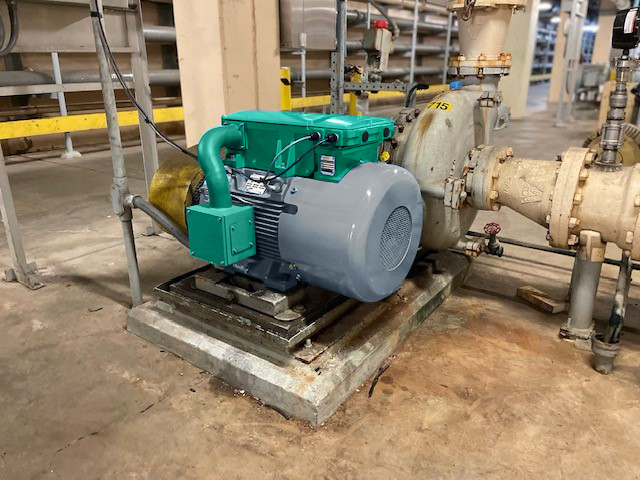
Long-Term Adoption and Expansion
Before testing VIDAR’s effectiveness, Met Council had ordered many traditional VFD units for one of their facilities. However, after experiencing the advanced savings, efficiency, and convenience of the VIDAR motor, they are now looking to expand VIDAR implementation to an additional 8-16 sludge pump units.