VIDAR Delivers Instant Results—A Fast Fix Without the Complexity of a VFD
A chemical company serving the agricultural market faced numerous issues with a chlorinator pump driven by a conventional fixed-speed motor. The pump, used for transferring a neutralized waste stream containing lime grit from the chlorinator vessel to a clarifier, was struggling due to a downstream control valve restricting flow. This restriction forced the pump to work harder, causing the motor to regularly run at 33 hp instead of its rated 30 hp, leading to excessive current draw, overheating, and wasted energy. Frequent shutdowns caused by overheating disrupted operations, increased maintenance costs, and reduced system reliability.
The Root Cause: Mechanical Inefficiency and Excessive Load
The control valve was consistently 40% closed, forcing the pump to work harder to maintain the required flow, which in turn increased the load on the motor. As a result, the motor drew 40 amps instead of the expected 35, generating excess heat that could shorten its lifespan by up to 50%. The restricted flow also caused turbulence, driving noise levels to 105 dB and creating a hazardous and uncomfortable work environment.
The Simple Fix: Swapping the Motor, Not Rebuilding the System
Instead of a costly traditional VFD installation, which would have required rewiring, new enclosures, and weeks of downtime, the company swapped the existing motor for VIDAR. Unlike traditional solutions, VIDAR embeds variable speed intelligence directly into the motor, eliminating the need for a separate VFD, inverter-duty cables, or external filters. Installation was as easy as replacing a standard motor and took just a few hours.
To achieve an immediate fix, the customer ran VIDAR in manual mode, adjusting the speed while keeping the control valve logic in place. After testing different speeds, they settled on 1600 RPM, which reduced power demand from 33 hp to 28 hp—well within the motor’s safe operating range—eliminating nuisance tripping and ensuring system reliability. Even more impressively, motor current draw dropped from 40 amps to 28 amps, a 30% reduction, due to both VIDAR’s near-unity power factor and lower power demand.
A Phased Approach for Even Greater Savings
While the customer’s primary goal was a quick and easy solution, they recognized that even greater efficiency gains were possible. In the near future, they plan to fully integrate VIDAR into their plant’s control system, allowing automatic speed adjustments based on demand. Once that’s done, they will eliminate the control valve entirely, unlocking even greater operational efficiency, system reliability and lifespan, and cost and energy savings.
Before
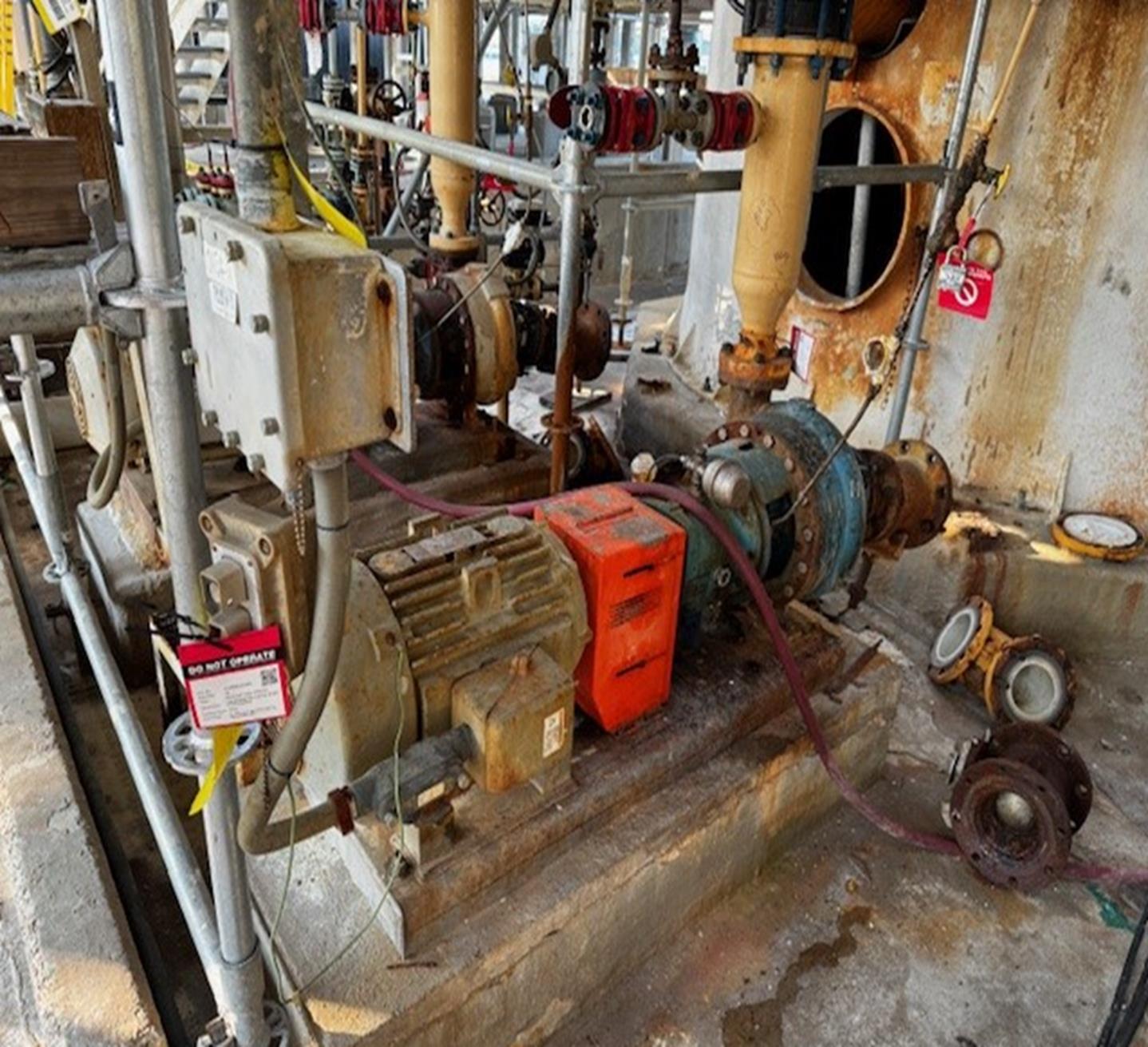
After
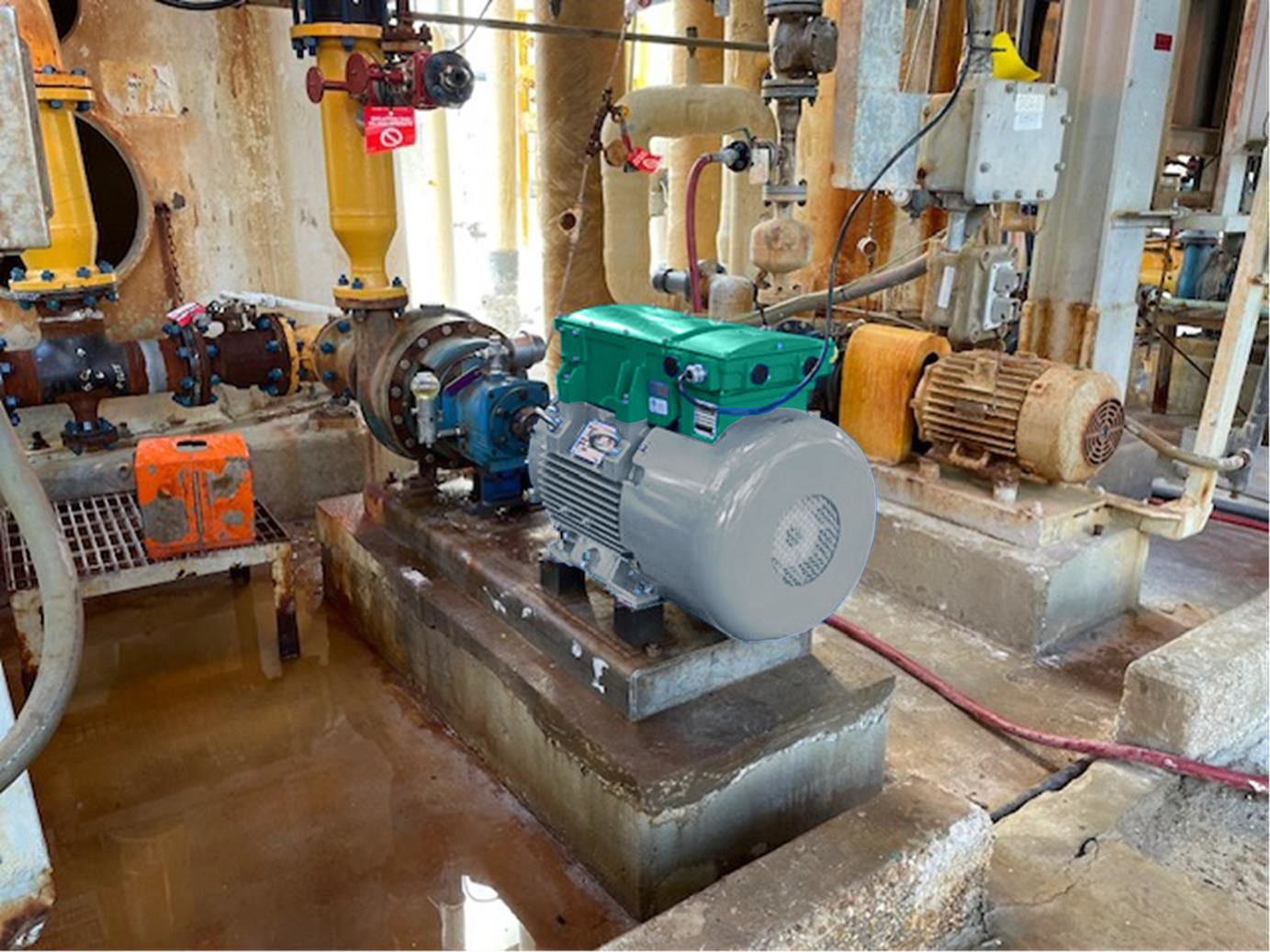
VIDAR vs. Traditional VFD Installation
A conventional VFD installation would have taken 4-6 weeks, while VIDAR solved the problem in just hours. In addition to the extended installation time, the total installed cost of a VFD was 40-50% higher than VIDAR, due to added expenses like inverter-duty cables, enclosures, and wiring modifications. This made VIDAR the clear winner in both time and cost savings. Following the success of this installation, the company is now expanding VIDAR to three additional chlorinator pumps, further enhancing efficiency and reliability across their operations
VIDAR Transforms How a Factory Runs
VIDAR isn’t just a motor—it’s a fast, easy, and effective solution. By embedding smart variable speed control directly into the motor, VIDAR eliminates the need for complex installations, reduces energy waste, and enhances system reliability.
What used to take weeks to fix now takes just a few hours. If your facility is struggling with energy waste, mechanical control inefficiencies, or unreliable pumps, the solution is as simple as swapping your motor.
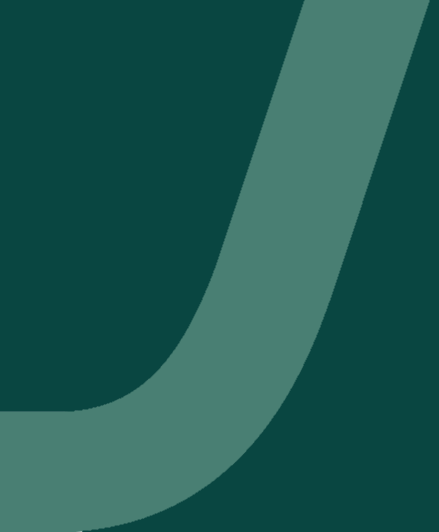