VIDAR Eliminates Costly Control Valve Repairs and Reduces Energy Consumption
A chemical company serving the agricultural market was facing escalating repair costs for a critical filter pump. The high pressure drop across the valve caused excessive vibration and turbulence, leading to repeated damage to a high-end valve and resulting in annual maintenance costs around $18,000.
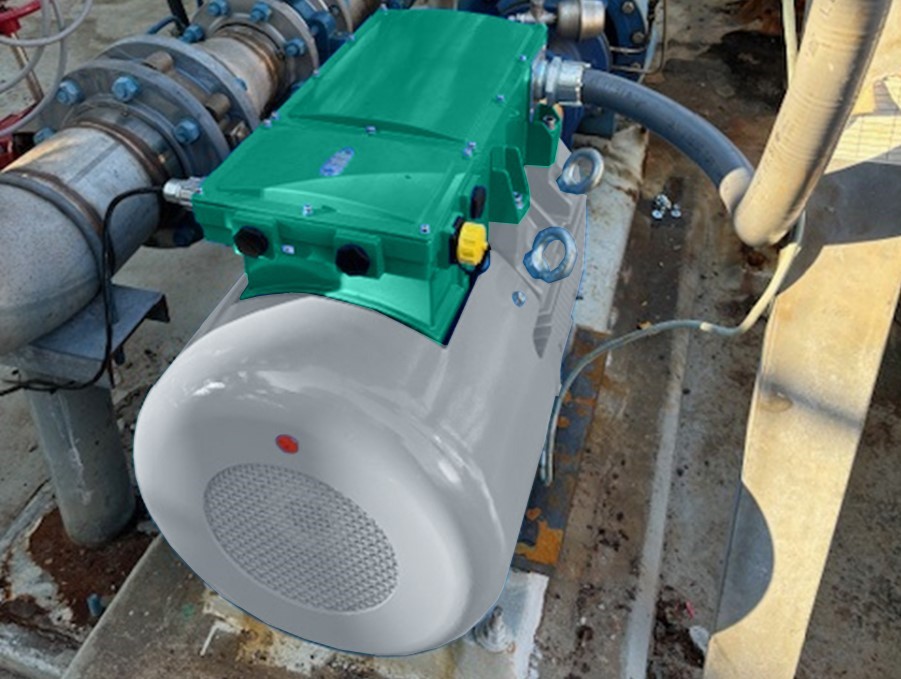
Operational Inefficiencies
The 60 hp pump’s control valve was consistently 60% closed, generating excessive noise and vibration due to constant valve chatter. Ambient noise levels around the pump ranged from 105 to 108 dB while operating at 1,750 RPM, creating both safety concerns and operational inefficiencies.
The company considered installing a variable frequency drive (VFD) to address the issue, but the nearest motor control center (MCC) would be more than 300 feet away. Implementing a VFD solution would require costly infrastructure modifications that would take a minimum of 3-4 weeks to implement.
The VIDAR Solution
As the company explored its options, the new VIDAR motor offered a timely opportunity to test an innovative alternative. VIDAR integrates variable speed intelligence directly into the motor, eliminating the need for external drives, complex wiring, and control centers.
The installation was completed within hours—far faster than the weeks required for a VFD implementation. VIDAR’s compact design allowed for seamless installation at the point of need, requiring only a single set of control cables for speed control.
Immediate and Measurable Results
The impact of VIDAR was realized immediately:
- Reduced Power: The pump’s control valve could now be fully opened, allowing for the same performance with a 50 hp motor instead of the existing 60 hp unit.
- Reduced Load: Pump speed was lowered by nearly 600 RPM, and current draw fell from 65 amps to just 28 amps.
- Reduced Noise: Ambient noise dropped from 105 dB to 81 dB, significantly improving workplace safety and comfortability.
Adding these reductions together, the company will see an annual energy savings of 149,200 kWh, saving the company $15,000 in energy costs alone. Add in the elimination of the annual control valve maintenance, and the company will save $33,000 every year. In this case, the annual savings means that the VIDAR motor will pay for itself in less than a year.
Long-Term Adoption and Expansion
Given both the savings and the impactful results achieved immediately with VIDAR , the chemical company quickly expanded VIDAR to another pump in the facility. Just two weeks after the second VIDAR was installed and delivered similar benefits, they placed an order for six more VIDAR motors, with the anticipation of many more to come.
VIDAR: A Simple, Smart, and Scalable Solution
VIDAR isn’t just a motor—it’s a fast, easy, and effective solution. By embedding smart variable speed control directly into the motor, VIDAR eliminates the need for complex installations, reduces energy waste, and enhances system reliability.
What used to take weeks to fix now takes just a few hours. If your facility is struggling with energy waste, mechanical control inefficiencies, or underperforming pumps, the solution could be as simple as swapping your motor.
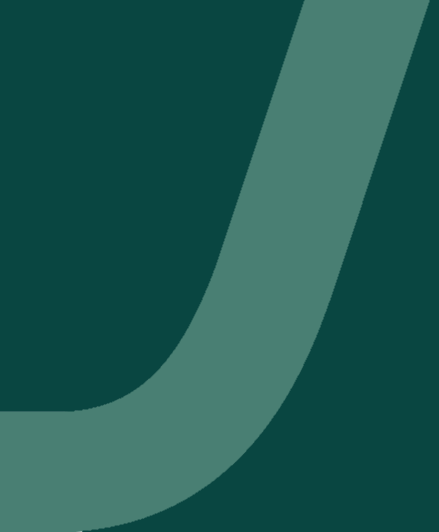