VIDAR Enhances Efficiency with Energy Savings at Large Agricultural Processing Plant
When VIDAR was presented to the plant engineering staff of Grain Processing Corporation (GPC), they quickly identified some practical benefits and inherent advantages as a novel approach to adjustable speed on pumps and fans.
According to Grain Processing Corporation (GPC) electrical engineer, Andrew Temple, “Upon learning of the VIDAR technology, we could immediately see several applications where this was a perfect fit. Working at a facility that is over 80 years old has its challenges in switch room real estate so having an all-in-one variable speed motor saved considerable money and time while still reaping the power savings and process control benefits.”
In fact, this is very common within the industry as VFD projects often require installation considerations that can be quite challenging and costly - especially when trying to retrofit an existing pump using a control valve to adjustable speed with a VFD. With VIDAR, there is no need for MCC room space, and it is estimated that total installed cost savings range from 30- 56% due to reduced materials, labor and engineering expenses compared to a traditional VFD.
According to Temple, “With the limited real estate driving the cost economics and installation complexity, it made sense to investigate the VIDAR solution further.”
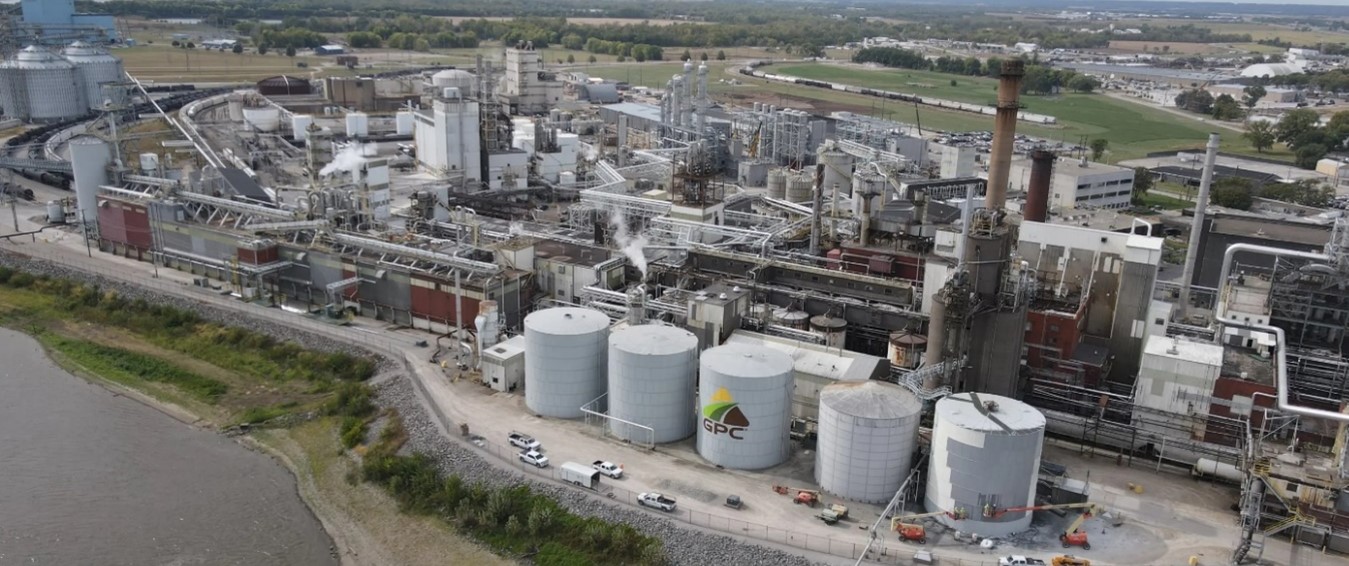
The decision was made to install VIDAR on a recirculation pump originally designed for a higher capacity. The application did not yet have a VFD as the electric motor driver was operating at full speed, and the pump discharge was fairly throttled back to achieve the needed flow rate of 1,050 GPM. After analyzing the process conditions, it was determined to be a suitable candidate due to the potential to reduce energy usage and indirect carbon emissions. It was also attractive because it was utilizing a 75 HP motor which was the original size motor developed by VIDAR.
VIDAR has demonstrated that power demand on fixed speed motors can typically be reduced by at least 50% through opening the control valve and lowering the operating speed to match the flow requirement. This was the strategy to be employed. An additional benefit construed by the plant engineers was the potential for ambient noise reduction. The location of the pump is in a small room which tends to amplify sound levels created by the throttled valve. Improving all aspects of the operation was the goal and VIDAR appeared to check all of those boxes.
Original Motor Installation on Recirculation Pumps
The VIDAR retrofit motor installation turned out to be very similar to a standard induction motor as the NEMA critical dimensions matched for a 365T frame. The equivalent 75 HP VIDAR dropped right into place. Once mounting was secured, the same coupling was used to connect the motor to the pump. The compact VIDAR unit, including the AC-Link power converter, appeared to be just like a severe duty rated TEFC motor. However, now there was integrated speed control and the ability to take a proportional reference signal from the DCS to regulate flow (GPM). This functionality does require an additional step: the installation of control wire and connection to the VIDAR Application Control Board (ACB) to receive the required I/O - very similar to a VFD. For this case, the control wire and conduit run were fairly reasonable with a distance of approximately 150 ft. A single analog speed reference is all that was required. There was no need for discrete signals as the plant engineer decided to use another unique VIDAR feature – maintaining the existing motor starter for start/stop commands to simplify the project even further. After some basic keypad programming, the VIDAR retrofit project was ready to operate.
Quantifying the results on this project proved to be helpful to understanding how VIDAR made a difference. The total installation and startup time was approximately 8 hours. The process variable set point was 1050 GPM, which would now be achieved with regulating pump speed while setting the control valve to 100% open. The operating speed was lowered from 1780 to 1360 RPM to match 1050 GPM. While energy savings is a primary objective, the physical wear and tear on all equipment components is significantly reduced as well when the demand power is lower. Some of these benefits take longer to evaluate over time in reliability calculations such as Mean Time Between Failure (MTBF.) However, there were many that could be measured and compared soon after the VIDAR motor went into service.
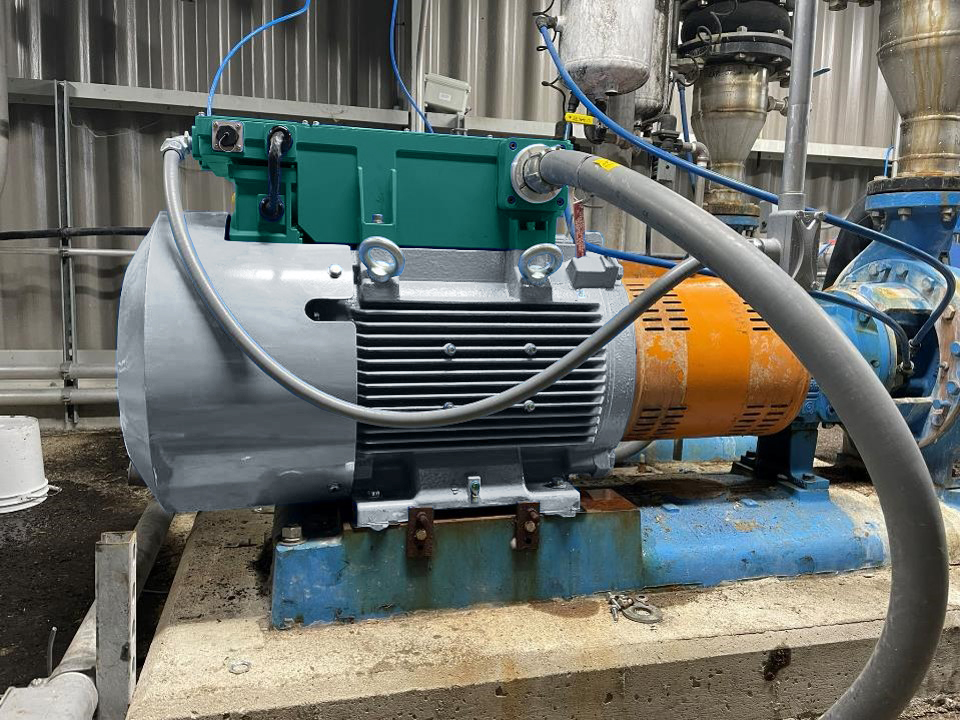
Power, current draw, energy savings, indirect CO2 emissions, annual equipment revolutions and audible noise could all be measured or reasonably calculated:
Results | Control Valve Fixed Speed | VIDAR Variable Speed | Savings |
Flow Rate | 1050 GPM | 1050 GPM | - |
Control Valve Position | 35% | 100% | 65% |
Speed | 1780 RPM | 1360 RPM | 420 RPM |
Ambient Noise | 103 dB | 80 dB | 23 dB |
Motor Current | 78.5A | 34.2A | 44.3 A |
Motor Power | 72.8 HP | 35.1 HP | 37.7 HP |
Annual Energy Cost | $34,318 | $16,558 | $17,760 |
Indirect CO2 Emission Reduction | 308 tons | 148.6 tons | 159.4 tons |
Revolutions Per Year | 854 million | 653 million | 201 million |
In the end, it was a seamless integration. The barriers and obstacles often encountered with VFD projects were overcome, and they found that VIDAR can be the bridge to operational excellence.
When asked about his perspective on the experience with VIDAR, Temple summed it up as, “After one year of the motor being in service, we have had vast improvement in process control as well as energy savings that has nearly paid off the entire cost of the motor. From an engineering, operations and maintenance perspective we are all firm believers in this new product. We’ve already purchased another and anxiously await putting it to work as well.”
For more than 80 years, GPC has provided superior grain-based products and exceptional service to iconic brands and companies worldwide. From Field to Family®, GPC uses corn, chickpeas, soy and other grains and pulses to craft high-quality ingredients used in the food, beverage, industrial, agricultural and pet care industries. Headquartered in Muscatine, Iowa, with facilities across the United States, GPC is a fourth-generation, family-owned business.
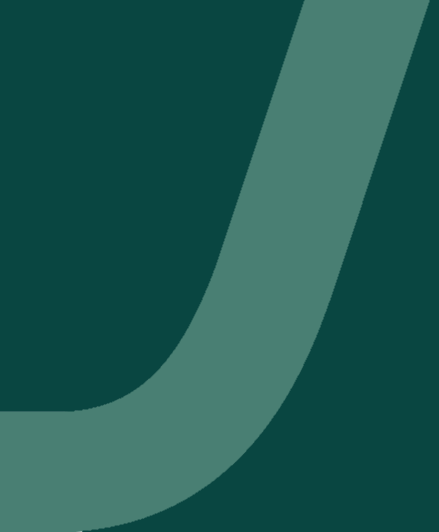